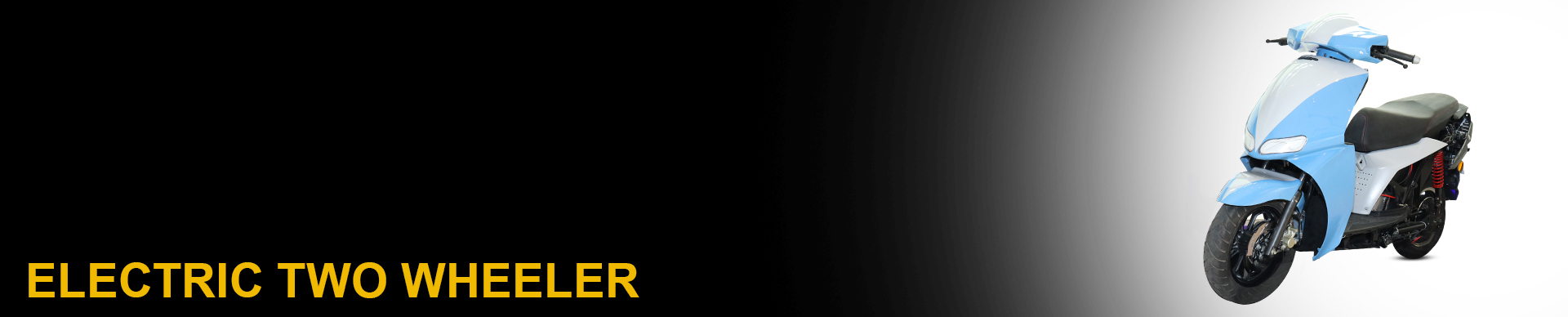
Electric vehicles signify the introduction of advanced technologies along with electric power components in vehicles. There are several risks associated with these technologies, such as thermal runaway of battery banks and fire, which need to be cautiously assessed. Numerous safety aspects need to be considered regarding vehicle electrification, including electric system safety, functional system safety, battery charging safety, and vehicle maintenance, operation, and training. The current challenges that hinder the popularity of electric vehicles are high battery cost, overheating, the total energy storage capacity of the battery, and the development of batteries for vehicles. Additionally, it is essential to examine the vehicle behaviour as these systems often fail, making them inefficient when compared to ICE vehicles. Thus, automobile manufacturers need to ensure that customers use systems that operate efficiently in varied conditions to effectively promote the use of these electrical systems and their components.
The electric two-wheeler set-up appears a lot more promising, in the form of research, financial acquisitions & investments, that makes the electric vehicle segment thrilling. Electric two-wheelers, by its swiftness and dexterity, easy operability and maintainability, affordability and low pollution, are most welcome among different categories of users. Mostly the customer segment that wants this change in pace includes city dwellers, short distance commuters, frequent road drivers and users of special needs. Besides personal use, electric two-wheelers also increasingly find their place in public service, such as urban sanitation, domestic and short distance patrolling, in delivery service, etc.
Key Distinguishers:
Transformed Product Development Process
The EV/HEV initiatives are facing lots of design challenges because of increasing dependency on electrical components and overall complexity, coupled with short design cycles. The challenge in working with simulation models & methods is the accuracy of the analysis data and results. This is further complicated by the uncertainty of electric vehicle and battery degradation profile. The objective of DEP’s research program is to extend model-based design with the integration of various component degradation modes and rates.
DEP Electric 2 wheeler Capabilities:
Electric Motor
- Electromagnetic Analysis
- Durability analysis
- Torque slip analysis
- NVH analysis
- Normal modes
- Force response
- NVH – radiated noise
- Durability
- Fatigue under external loads
- Thermal and cooling
- Coolant flow analysis
- CHT
Battery and Inverter:
- Pressure drop
- Full pack thermal analysis
- Hard short
- Max.withstandable voltage
- Ripple & Electro-Thermal
- Torsional and Bending analysis
- Seal analysis
- Cell expansion
- Side pole – Crash
- Pot hole
- Bolt sequence analysis
DEP Advantages:
Building hardware is a great art that requires time and a lot of procedures & guidelines. But evaluating the machine model by connecting them to circuit models is the new extraordinary experience that DEP can provide. With its wide range of simulation solutions for complex EV/HEV powertrain design, DEP makes a significant impact on performance & efficiency of the overall product. Refining the electric motor operation map, battery charge/discharge maps and vehicle dynamics model determining the Complete Modeling process
Customer Benefits: